制御盤自動配線システムへの夢:全自動電線加工機
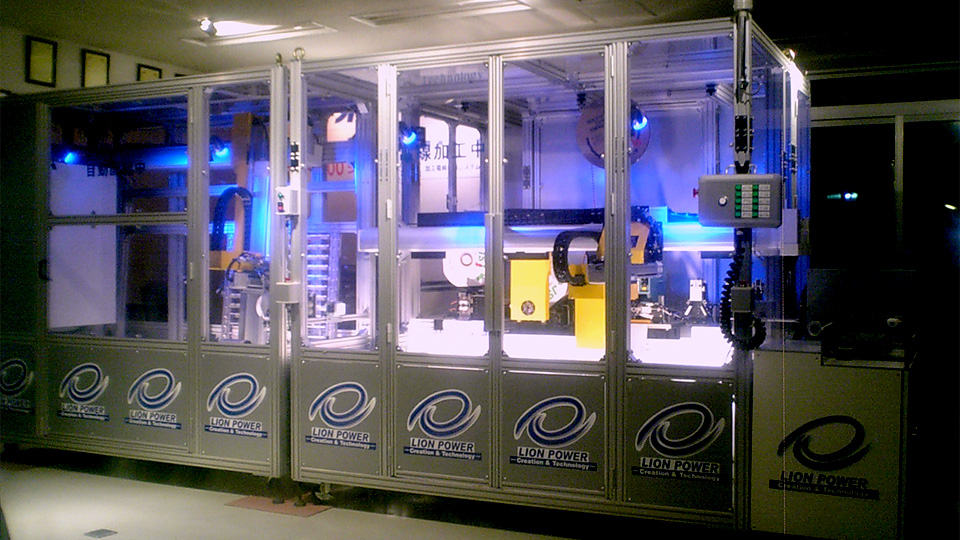
3人の創業メンバーがメーカーへの夢を託した製品開発テーマ。
1人の電気技術者から始まり、困難なマーカーチューブの自動挿入を実現。今では全国のお客様にご利用いただき、制御盤製造の新文化創造へと歩みを進めています。
“技術を楽しむメーカー”とは何だろう?
1985年頃、ライオンパワーは工場の生産性向上を目的とした自動化ロボットシステムなどを手がけていました。
自動化に貢献する「直行ロボット」「多関節ロボット」などを製造しお客様にお納めしているのに、自社の製造現場ではロボット自体をハンドメイドで製造している…。会社としてそんな違和感を覚えていた時代でした。
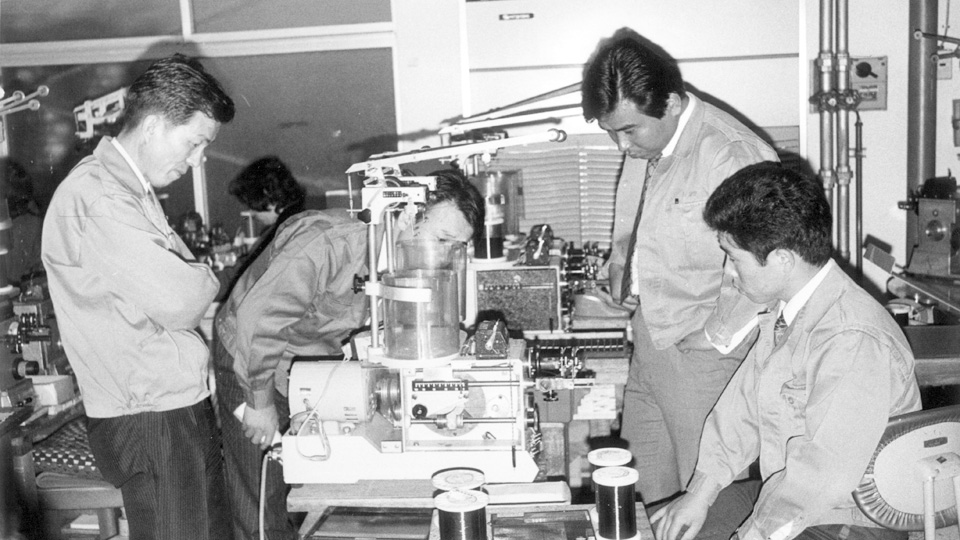
ある日、火力発電所の制御盤製造をさせていただいたのですが、発電所の制御盤ともなるとハーネス加工の多さも尋常ではなく、非常に手こずる作業となっていました。
このあまりの手間のかかりようが、ふと自動化ロボットの発想を呼び起こしたのです。
「制御盤を自動で製造するシステムを開発しよう!」
創業当時からのライオンパワーのビジョンは『技術を楽しむメーカー』。“大手企業様から仕事を頂きお納めする”という下請け仕事をこなしている自分たちはいま、技術を楽しんでいるのか。はたして“技術を楽しむ”とはどういうことなのか…。
『制御盤自動配線システムの開発』というのは、単に研究開発テーマというだけでなく、ライオンパワーの設立目的を実現するためのプロジェクトだったのです。
マークチューブに電線を通す難しさ
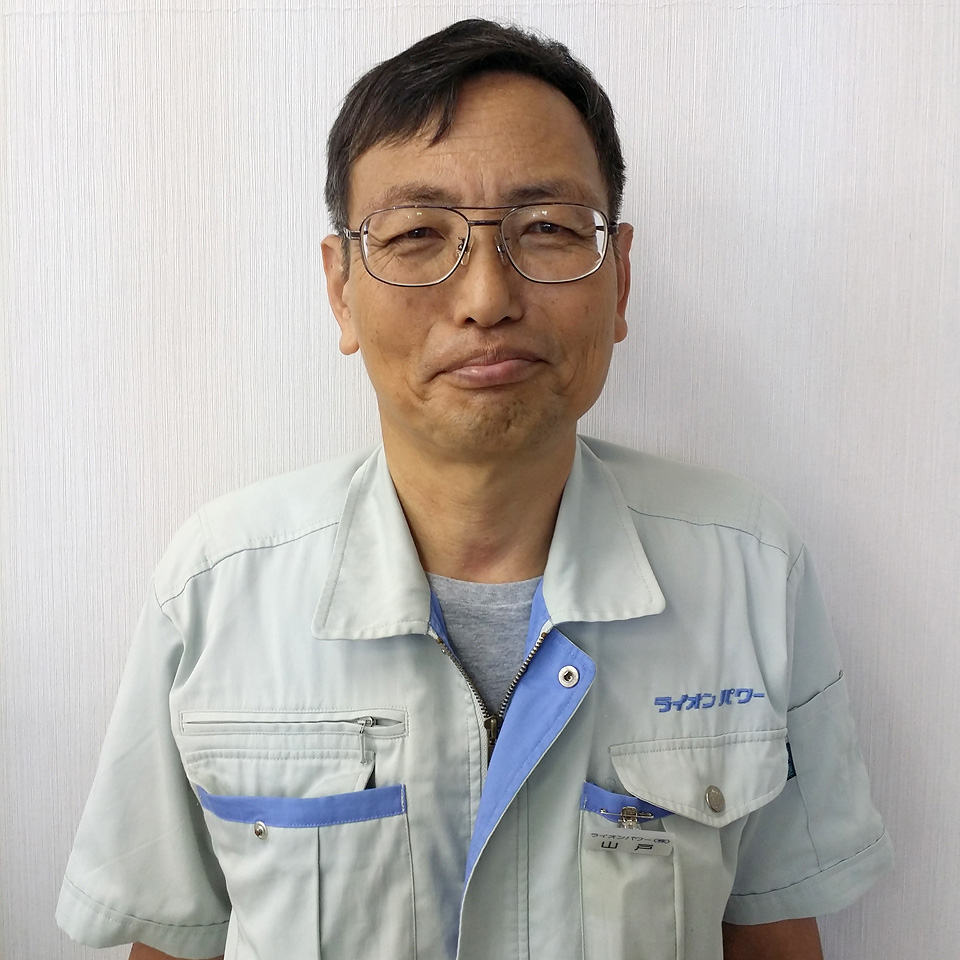
開発当初の問題は人材でした。
仕事の合間に開発を行うことでスタートはしたものの、仕事が忙しい時は社長も関係なく生産の手伝いをするほど。開発に取り組める時間ができたとしても、「時間がある=仕事がない」ということで、結局は営業に駆け回る状態に。
“忙しくても暇でも開発には取り組めない”ということがわかり「専門の開発要員を採用しよう」ということになったのです。
このとき採用されたのが、金沢工業大学工学部電気科を卒業した山戸博一でした。
ところが、電気技術者一人でロボット開発などというのはどだい無理な話。最初の6年間は、機械設計、ソフトウェアの勉強ばかりの日々でした。
勉強を一通り終えて“いざ開発”となったとき、電気・機械・ソフトウェアというロボット開発のための知識全般を蓄えた山戸は、このテーマの本当の難しさを目の当たりにするのです。
制御盤の自動配線への第一歩は、配線するハーネスの自動製作でした。
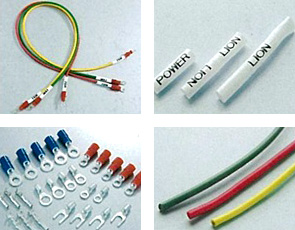
ところがハーネスと一言で言っても、電線はくねくね曲がり、ハーネスを通すマークチューブは「筒」だとはいえ、潰れたりひしゃげて変形している状態。
マークチューブに電線を通す作業は、人間の手作業ならチューブの変形を補正しながら挿入できても、機械が行うのは非常に困難。いきなり高度な難題が立ちはだかりました。
マークチューブにハーネスを通すためには、様々なマークチューブの一様ではない変形を補正する必要がある。
「ひしゃげた筒を“正円に近づける”方法を考えよう。」
アイディアは良いけど遅いねぇ〜
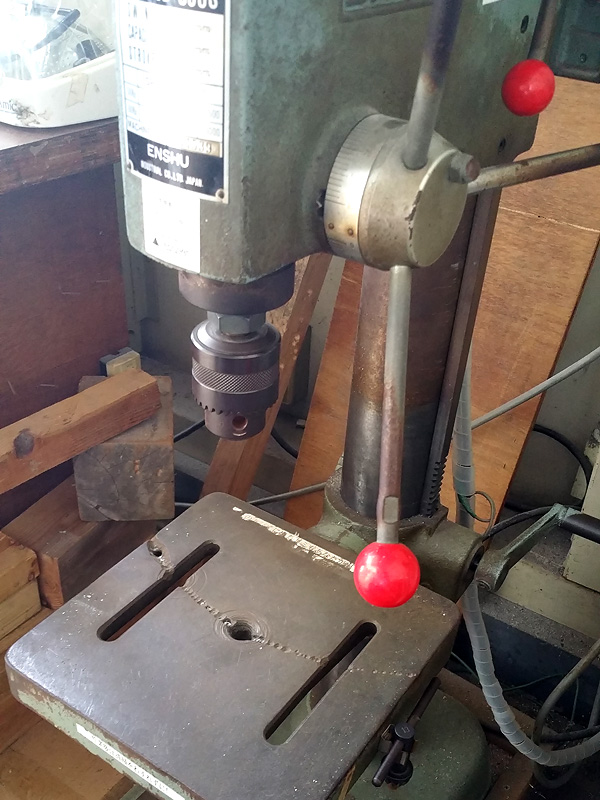
ひしゃげたマークチューブを正円に近づけるアイディア。それはボール盤の三つ爪チャックとチップ部品を載せるマウンターの部品傾き補正機の利用でした。
マークチューブを円筒爪で保持させることで、潰れや変形をある程度正円に近づけることができたのです!
マークチューブが正円になることでハーネスを通す成功率が格段と上がり、ハーネスの自動加工にも目途がたちました。このユニットは現在「チャックユニット」と呼んでいますが、弊社が特許権を取得しており今でも装置の心臓部を構成。業界Only One方式となっています。
そして完成した最初の装置が、半自動の電線加工機「HI-1000」。配(はい)→HI、線(せん)→1000。そのものズバリ「配線」という名前を冠しました。
意気揚々と展示会に出展したものの、お客様の反応は「アイデアは非常にいいけど、遅いね~!」がほとんど。成功率も100%でなかったために、導入には消極的な発言ばかりでした。
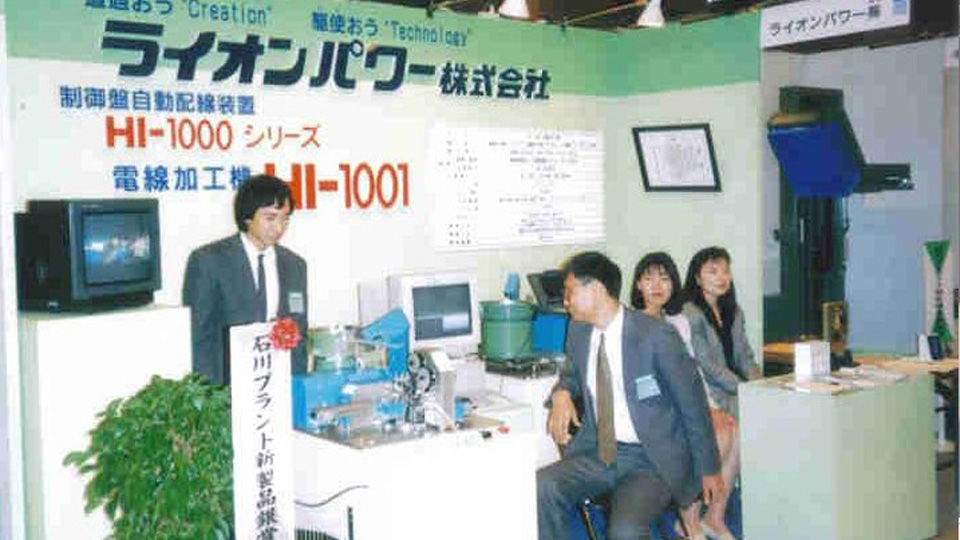
それもそのはず、制御盤製造業界ではハーネスに1本不良が出たとなれば、何百、何千もある制御盤内の全てのハーネスをチェックしなければなりません。リスクがメリットを大幅に超えていたのです。
細かい部品の形状や長さの変更など様々な改善を加え、成功率をアップさせる。これが当面の目標となりました。
技術を楽しむメーカーは常識を覆す??
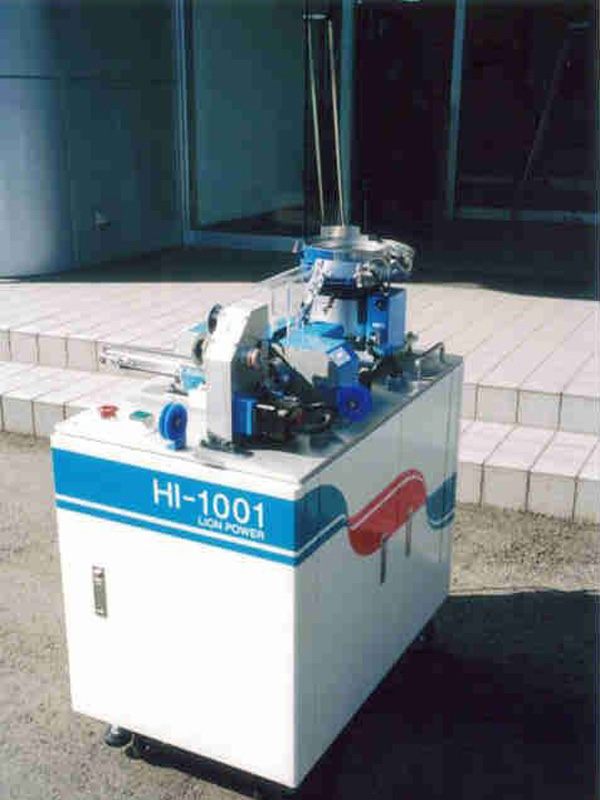
まだ半自動機が2セットしか売れていない当時、装置を見たとある大阪の企業(S社)様から「全自動機が欲しい」とのお声をいただきました。
このお客さま曰く、『ハーネスのマークチューブを入れることが出来て、端子も圧着できる装置はライオンパワー社製しかない』とのこと。弊社の技術力を高く評価いただけたのです。
一方その当時まだ弊社には半自動機の開発実績しかなく、開発部隊は全自動機には消極的。しかし、『技術を楽しむメーカー』の実現に向かって、全自動に取り組むことは自然の流れでした。
試作機を設計製造するのではなく、お客様が実際に使用する製品を開発する。研究開発メンバーのモチベーションは高い一方、今だから言えるのですが「できるかどうか」というかなりの不安をかかえていたのも事実です。
開発した試作機は、HI-1000に1をプラスした「HI-1001」。最大の特徴は、中央部にあるチャックユニットが回転することでした。
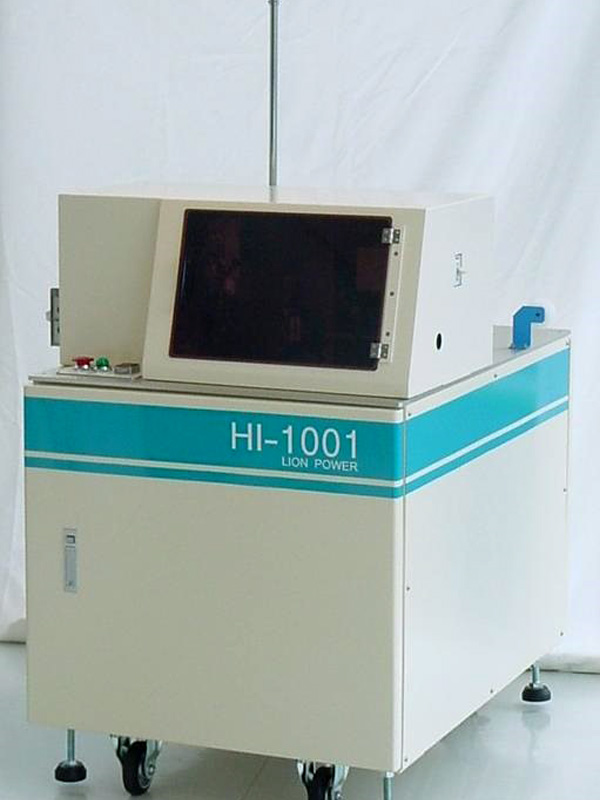
交差点を整理する警察官のように、後ろから来るマークチューブを受け取り、右に方向を変えてハーネスを通し、向きを変えて端子を圧着する、という画期的な機械構成。
アイデアが非常に良かった一方、耐久性や精度に問題があったため製品化での採用は見送られました。
しかし試作機のこのアイデアは販売機で活かされます。
販売機では“くねくね曲がったハーネスを真っ直ぐにして送る”というこれまでの常識を覆し、わざとハーネスを曲げる方法を採用。これにより試作機よりも25%のコンパクト化も達成したのです。
販売機の実現にほっと胸をなで下ろし、大阪のS社様にこの装置を販売。
しかし実はこれが波乱の第二幕の幕開けだったのです。
お客様に教わり続けた一年半
何よりも大きかった問題は、お客様は『全自動なのだからどんな理由であろうが常に動き続ける』という考え、一方弊社は『材料の状況や加工ミスなどで機械は一時停止する』という考えを持っていたことでした。実際この装置では、加工ミスでのハーネス廃棄時に装置が停止することがありました。
また、ハーネスへのこすり傷の処置と測量精度の調整という問題もありました。
例えば、ハーネスをしっかり速く送るために付けたローラーの溝。一方でこの溝はハーネスにこすり傷を付けることにもなるので、傷がつきにくく滑りにくい溝デザインを見つける必要がありました。
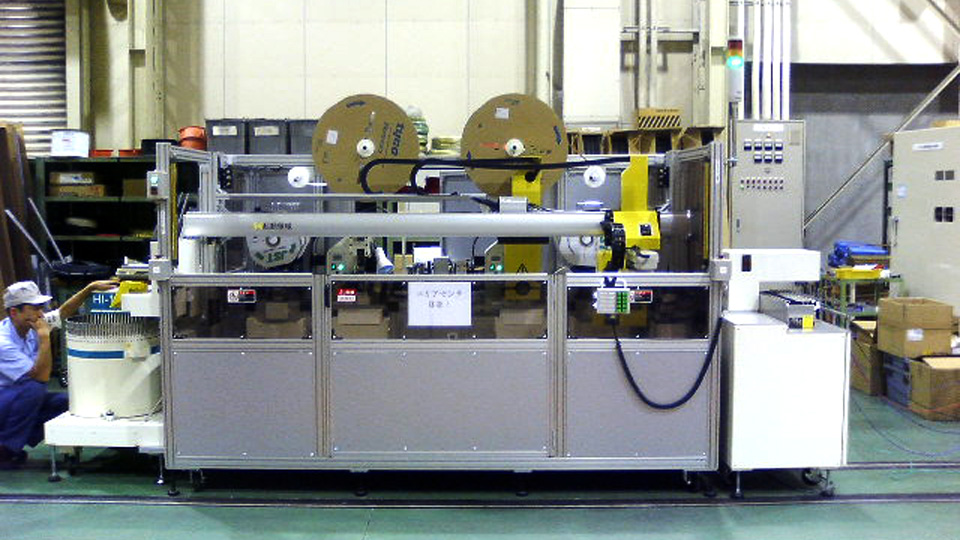
開発側はどうしても緩い基準で考えがち。弊社でのOKという判断は、必ずしもお客様のOK判定とはならなかったのです。
このような『開発段階で解決しておかなくてはいけない項目』が次々と指摘され、それを順次解決していくということが、なんと“一年半”も続きました。
当時の主力メンバーは技術者の山戸、北森、和佐田、営業を担当していた現社長の高瀬。皆若く勢いがあったため乗りこえることができたのかも知れません。
この時のお客様からの長期にわたる数多くのご指導(ご指摘)があったからこそ、現在の全自動電線加工機「HI-2000」を生み出せたと言っても過言ではありません。
あまりにもご指導いただく場面が多かったため、上記のお客様に「この機械はライオンパワーとうちとの共同開発ですか?」って真面目に言われたことも(笑)。
制御盤製造の新しい文化が誕生
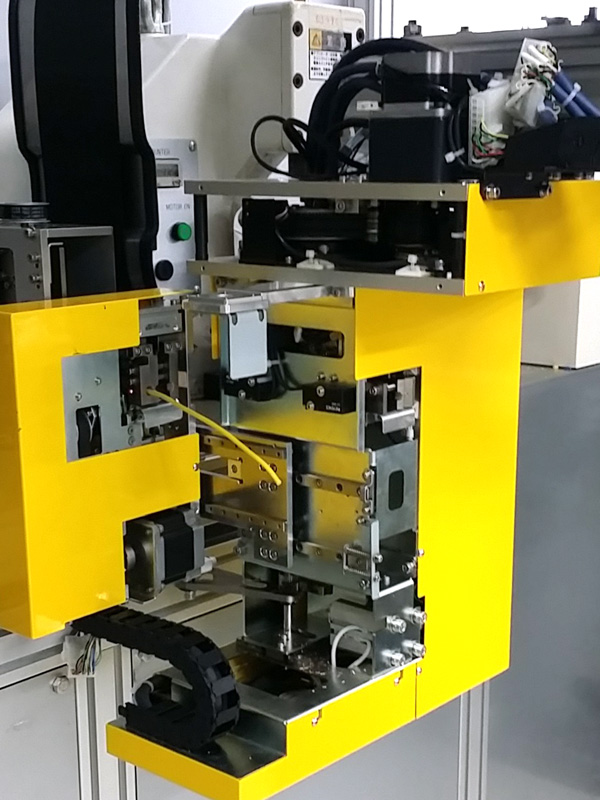
この装置は、これまで1週間かかっていた制御盤製造を2日間に短縮したことが評価され、最終的にはユーザー様の社内賞『社長賞』を頂いたようです。
このお客様には「現場の若いやつらは、ハーネスは自動で出来るものと思っている」「昔は1本ずつ作っていたのにね~」というお言葉もいただきました。これは、私たちが目指している制御盤製造の新しい文化が誕生した瞬間ともなりました。
このお客様にはその後、2号機、3号機も購入して頂いています。
2号機(HI-2000バージョン)は、HI-1001での問題点を克服し、molexやAMPといったコネクタ端子の圧着など対応端子の種類を大幅に増やし、なおかつユーザー別の特注設計を容易にする形へと進化させました。この仕様がヒットし、その後毎年のように2~3台売れるようになっています。
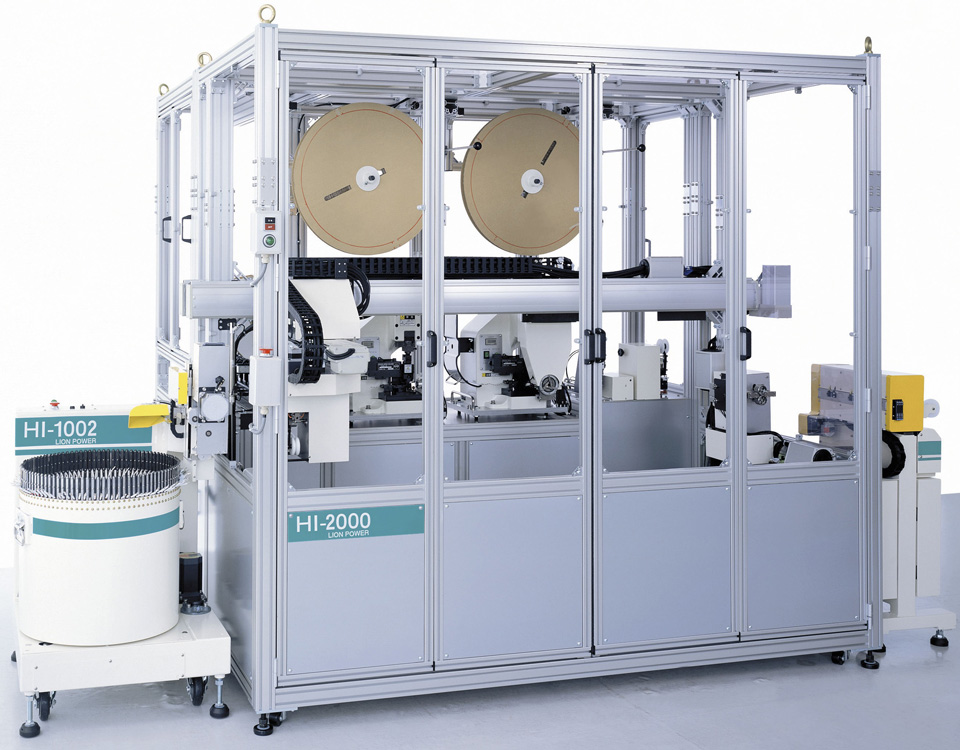
毎年のマイナーチェンジでは、対応端子、電線種類を増やしていますが、最近では150mmの渡り線も自動で製作できるようになりました。これもプチヒット状態であり、装置購入済みのお客様も改良して導入していただくこともあります。
大型の特注品のご依頼も多く、制御盤製造用の電線加工機業界にてライオンパワーの存在感が出てきました。
今後もライオンパワーの電線加工機にご期待下さい。

加工スピード大幅アップ。ハーネス作成15秒/本!!
量産型ユーザ様に最適な超速全自動電線加工機!
HI-3000 !!

電線カット・マークチューブの印字と挿入・被覆剥き・端子圧着…。まだ手作業ですか?
リードタイム短縮&コスト削減の救世主!

「とまつくん」なら、ボタン一つで簡単に均一で美しい塗抹標本を作成できます!!